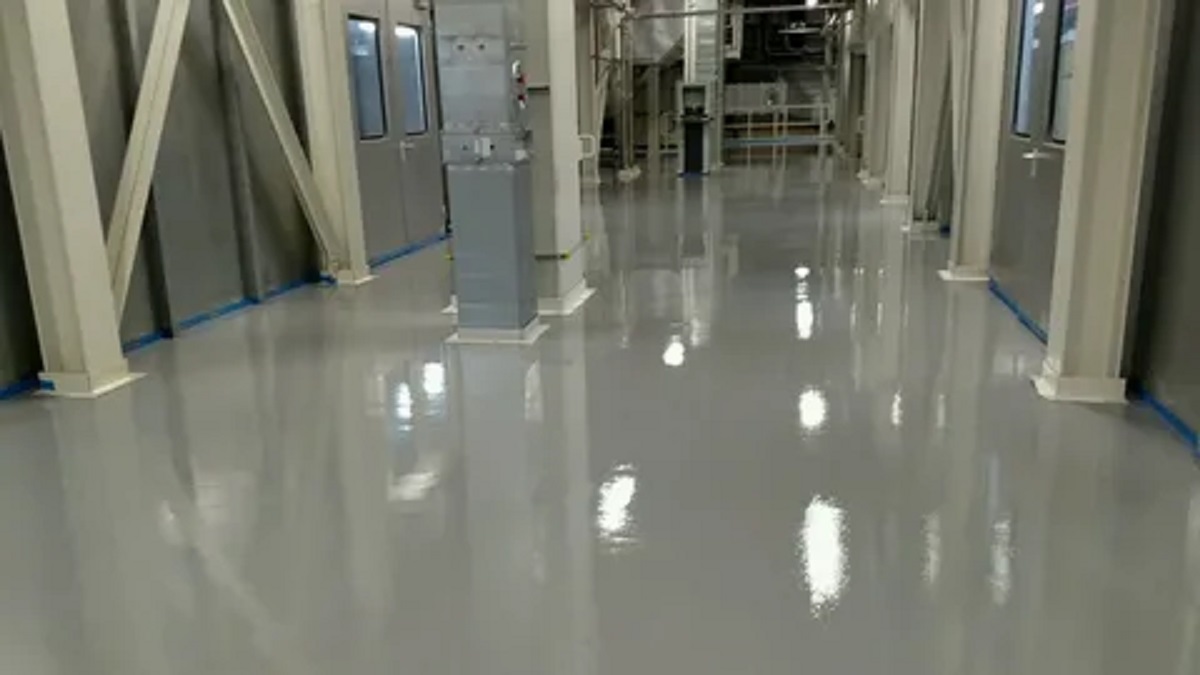
What Are The Best Methods For Applying Anti-Static Coating?
Anti-static coatings help prevent static electricity and are used on electronics and plastic. The best methods to apply them include spraying, brushing, dipping, and rolling. Spraying is quick and easy, using a spray can or gun to spread the coating evenly, ideal for large areas. Brushing is good for small areas, providing control but can be slow. Dipping involves submerging the object into the coating. This ensures full coverage. It is best for small to medium items.
Rolling is suitable for flat surfaces, offering quick and even coverage. Before applying, clean the surface, making sure it is dry and dust-free. Always follow the product instructions for better and longer-lasting results.
Benefits Of Anti-Static Coating
· Anti-static coating prevents dust buildup on objects, keeping them cleaner.
· It reduces static electricity that can harm electronic devices.
· Surfaces with anti-static coating are easier to clean and maintain.
· Touching materials treated with this coating prevents unpleasant shocks.
· Screens benefit from anti-static coating by improving visibility and reducing fingerprints.
· It extends the lifespan of electronics by minimizing static interference.
· In manufacturing, anti-static coating prevents damage during production and assembly. It promotes safety in sensitive environments.
How Spraying Works For Anti-Static Coating
Spraying works for anti-static coating by using a special spray gun. The gun sprays a thin layer of the coating onto surfaces like plastic or glass. This coating stops things from building up extra electricity. It keeps them from getting too charged. The spray covers the surface evenly. This helps the coating stick well. When the coating dries, it forms a smooth layer. This layer stops static electricity from collecting. It’s like putting on a thin, invisible shield.
This shield stops things from clinging or sparking. Industries use this process to make electronics safer. It’s also used on car parts and packaging materials. Spraying anti-static coating prevents static electricity problems.
Using Brushing For Anti-Static Coating
Brushing is a way to apply anti-static floor coating to surfaces. It uses a brush to spread a special substance that prevents static electricity. This coating stops static electricity from building up. When you brush on this substance, it sticks to the floor. This makes the floor less likely to create sparks when you walk or move objects. It’s important in places with lots of electronic equipment. These areas need to avoid static because it can damage sensitive devices. Brushing ensures the coating covers the whole floor evenly.
This method is effective for small to medium-sized areas. It’s also affordable compared to other methods. We use brushing for anti-static coating. It makes floors safer in places like labs, factories, and computer rooms.
Dipping Methods For Anti-Static Coating
Dipping methods are ways to coat things in liquids. They work by dipping things into a liquid to cover them. When you use dipping with anti-static concrete sealer, you cover concrete. This is to prevent static. This sealer stops static electricity from building up. It’s important for places where static can damage equipment or hurt people. Dipping with anti-static concrete sealer means submerging concrete into the liquid. This coats the concrete evenly. After dipping, the sealer dries and forms a protective layer. This layer keeps static electricity away.
Industries often use this method to protect floors and surfaces. It helps maintain safety and protects costly equipment from static damage. Using dipping methods with anti-static concrete sealer is smart. It safeguards workplaces. It’s a simple but effective process to ensure a safer environment.
Rolling Techniques For Anti-Static Coating
The techniques for rolling on anti-static coating involve spreading a special material. This material prevents static electricity. Workers apply this coating using a rolling tool that spreads it evenly. The goal is to cover surfaces completely, like floors or machines. This helps to stop static electricity from building up. Imagine rolling paint onto a wall; it’s a bit like that, but with a different material. These techniques ensure that the coating is smooth and effective. When machines or floors have this coating, they are less likely to create sparks or shocks. This is important in places with static electricity.
It can cause problems in places like factories or labs. By using rolling techniques, workers make sure that every part gets covered properly. This helps keep things safe and running smoothly, without any unexpected static surprises.
Preparing Surfaces For Anti-Static Coating
Preparing surfaces for an anti-static concrete sealer involves getting them clean and smooth. First, you need to clean the concrete well. This means removing dirt, oil, and any old coatings. Scrubbing with soap and water can do this. After cleaning, the surface must dry completely. Then, check for rough spots or cracks in the concrete. These can be filled or smoothed out using a patching compound or grinder. Once the surface is smooth, apply the anti-static concrete sealer evenly. This coating helps prevent static electricity from building up on the floor.
It also protects the concrete from stains and damage. After applying the sealer, let it dry according to the instructions. This gives the best results. It also gives a finish that lasts a long time. The finish keeps the floor looking good and safe from static.
Common Mistakes To Avoid With Anti-Static Coating
When applying anti-static floor sealer, it’s important to avoid common mistakes. One mistake is not cleaning the floor properly before application. Dirt and dust can prevent the sealer from sticking well. Another mistake is applying the sealer too thickly. This can lead to uneven coverage and longer drying times. It’s also crucial not to rush the drying process. Letting the sealer dry completely ensures it works effectively. Sometimes people forget to apply a second coat for extra protection. This can reduce the sealer’s effectiveness. Lastly, the wrong applicator can leave streaks. It can also leave uneven layers of anti-static floor sealer. Avoid these mistakes. Follow the application instructions carefully. Doing so can maximize your anti-static coating’s effectiveness. It will keep your floors protected and safe from static buildup.
Maintaining Surfaces With Anti-Static Coating
Maintaining surfaces with anti-static coating helps prevent static electricity from building up. Best floor coatings like these keep floors smooth and prevent dust from sticking. They are useful in places with lots of electronics, like offices and labs. Anti-static coatings also protect sensitive equipment from damage caused by static electricity. Regular cleaning is important to keep the coating effective. It’s like giving your floors a shield against electrical shocks.
These coatings make floors easier to clean and safer to walk on. They create a barrier that reduces the chance of sparks that could harm machines or people. Choosing the best floor coatings means thinking about how often the floor gets used. You also need to consider what it’s used for. They are a smart way to keep everyone safe and keep floors looking good.
Related: WHY CHOOSE POLYASPARTIC FLOOR COATING OVER EPOXY?