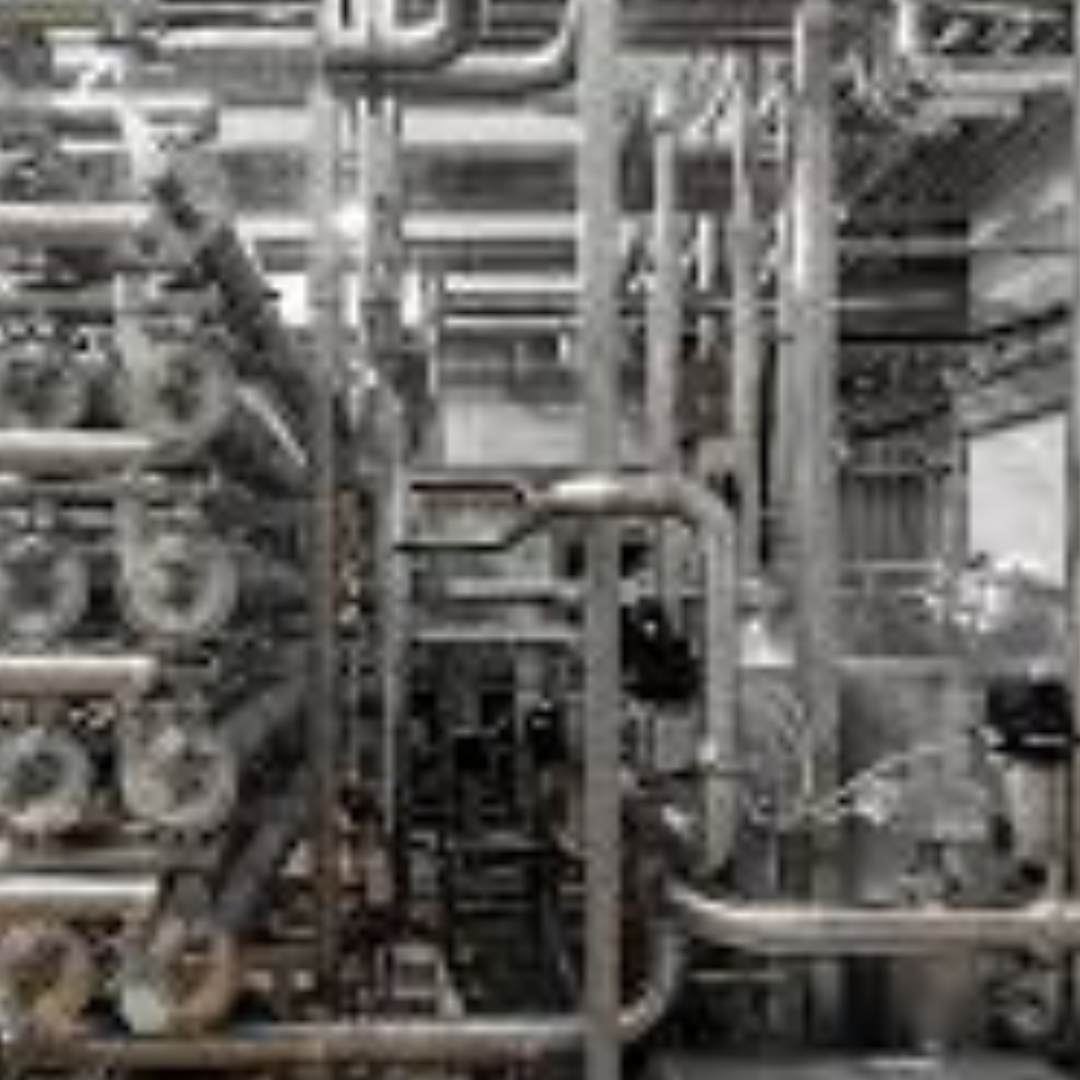
The Importance and Innovations in Semiconductor Piping and Semiconductor Process Piping
The semiconductor industry is the backbone of modern technology, driving advancements in various fields including computing, communications, and consumer electronics. A critical yet often overlooked component of semiconductor manufacturing is semiconductor piping and semiconductor process piping. These systems are integral to the production process, ensuring the safe and efficient transport of gases, chemicals, and other materials essential for semiconductor fabrication. This blog explores the importance of semiconductor piping, the latest innovations in the field, and best practices for maintaining these vital systems.
The Role of Semiconductor Piping
Semiconductor piping systems are designed to handle the precise and controlled flow of ultra-pure gases and chemicals required in semiconductor manufacturing. These materials are used in various processes such as chemical vapor deposition (CVD), plasma etching, and photolithography. The purity of these substances is crucial, as even the smallest contamination can lead to defects in the semiconductor wafers, compromising the performance of the final products.
Key Functions of Semiconductor Piping:
-
Material Transport: Semiconductor piping ensures the seamless transport of critical materials from storage tanks to the production equipment.
-
Containment: These systems provide robust containment to prevent leaks and ensure the safe handling of hazardous chemicals.
-
Precision: Advanced piping systems maintain precise control over the flow rates and pressures, which is essential for consistent manufacturing quality.
Innovations in Semiconductor Piping
The semiconductor industry continually evolves, and so do the technologies and materials used in semiconductor piping. Innovations in this field aim to enhance efficiency, safety, and reliability, ensuring the production of high-quality semiconductors.
Advanced Materials
One of the most significant advancements in semiconductor piping is the use of new materials that offer superior performance and longevity. Polytetrafluoroethylene (PTFE), fluorinated ethylene propylene (FEP), and other high-performance polymers are increasingly used due to their exceptional chemical resistance and purity. These materials minimize the risk of contamination and are capable of withstanding the harsh conditions of semiconductor manufacturing.
Modular Piping Systems
Modular piping systems are becoming more popular due to their flexibility and ease of installation. These systems allow for quick assembly and disassembly, facilitating maintenance and upgrades without significant downtime. Modular systems also enable manufacturers to scale their operations more efficiently, adapting to changes in production demand.
Enhanced Monitoring and Control
The integration of advanced sensors and control systems has revolutionized semiconductor process piping. Real-time monitoring of flow rates, pressure, and chemical composition ensures optimal performance and immediate detection of anomalies. Automated control systems can adjust parameters dynamically, maintaining consistent production quality and reducing the risk of human error.
Cleanroom Compatibility
Given the stringent cleanliness requirements in semiconductor manufacturing, piping systems are now designed with cleanroom compatibility in mind. This involves using materials and construction techniques that minimize particulate generation and simplify cleaning processes. Innovations in cleanroom-compatible piping help maintain the ultra-clean environments necessary for high-yield semiconductor production.
Best Practices for Semiconductor Process Piping
To maximize the efficiency and reliability of semiconductor process piping, manufacturers should adhere to best practices in design, installation, and maintenance.
Design Considerations
-
Material Selection: Choose materials that offer the highest purity and chemical resistance suitable for the specific chemicals and gases used in the process.
-
Flow Control: Implement precise flow control mechanisms to maintain consistent delivery of materials.
-
Redundancy: Design systems with redundancy to ensure continuous operation in case of component failure.
Installation Guidelines
-
Cleanroom Standards: Follow cleanroom standards during installation to prevent contamination.
-
Proper Jointing: Use appropriate jointing techniques to ensure leak-proof connections.
-
Testing: Conduct thorough testing of the piping system before it becomes operational to detect and rectify any issues.
Maintenance Strategies
-
Regular Inspections: Schedule regular inspections to identify wear and tear or potential leaks.
-
Preventive Maintenance: Implement a preventive maintenance program to replace aging components before they fail.
-
Cleaning Protocols: Establish strict cleaning protocols to maintain the purity of the piping system.
Case Studies of Semiconductor Piping Excellence
Case Study 1: Advanced Micro Devices (AMD)
AMD, a leading semiconductor company, recently upgraded its semiconductor process piping systems in its flagship facility. By incorporating modular piping and advanced materials, AMD significantly reduced downtime during maintenance and enhanced the overall efficiency of its production processes. The integration of real-time monitoring systems allowed AMD to detect and address issues promptly, ensuring consistent production quality.
Case Study 2: Intel Corporation
Intel Corporation has long been at the forefront of semiconductor manufacturing innovations. In its latest facilities, Intel employs cutting-edge semiconductor piping systems with enhanced cleanroom compatibility. The use of automated control systems and advanced sensors has enabled Intel to maintain ultra-high purity levels and optimize material usage, contributing to higher yield rates and lower production costs.
The Future of Semiconductor Piping
As the demand for semiconductors continues to grow, driven by advancements in AI, IoT, and other emerging technologies, the need for efficient and reliable semiconductor piping systems will only increase. Future innovations are likely to focus on further enhancing material purity, improving modularity, and integrating even more sophisticated monitoring and control systems.
Researchers are exploring new materials and coatings that could offer unprecedented levels of chemical resistance and durability. Additionally, advancements in IoT and AI could lead to the development of smart piping systems capable of self-diagnosis and autonomous maintenance, further reducing downtime and operational costs.
Conclusion
Semiconductor piping and semiconductor process piping are crucial components of the semiconductor manufacturing process. The innovations and best practices in this field ensure the production of high-quality semiconductors, meeting the stringent demands of modern technology. By continuing to invest in advanced materials, modular systems, and enhanced monitoring, the semiconductor industry can achieve greater efficiency, safety, and reliability in its manufacturing processes. As we look to the future, the continued evolution of semiconductor piping will play a vital role in supporting the next wave of technological advancements.